Accounting Wilkerson Company Case Instructions
Question :
In a business memo, answer the following questions, directing your responses to Robert Parker, the president of Wilkerson Company. Keep your answers succinct. Assume that Mr. Parker knows all of the background information, so there is no need to repeat it. Your memo should be no more than three pages, single spaced (two for the memo, one for calculation tables).
1. What insights does ABC provide over the current overhead allocation method?
2. What are the cost allocation rates using ABC at full capacity (as compared to actual capacity)? There’s no need to actually allocate overhead using the full capacity rates. Just calculate the full capacity cost driver rates for each activity (for example, $30/machine hour for machine related expenses for actual capacity).
3. Should Wilkerson use actual capacity or full capacity costs under the ABC method? Why?
4. What suggestions do you have for Mr. Parker and Wilkerson Company? Be specific, with support for your answers.
Answer :
To, Robert Parker
From: ( Put Your name)
Subject: Application of ABC costing for overhead cost allocation.
Based on the previous financial measures undertaken by the company, the profitability for Wilkerson has become unpredictable and unstable. Therefore, when reviewing the cost allocation of the current products, it is being identified that the company is using the traditional technic for the overhead’s calculations. The cost allocations depending on the production units is not a valid for the overheads allocation. Currently, the Activity-based costing is greatly used in the overhead’s allocation as per which the cost is being allocated to the production units among various products based on their activity consumption denoted by the activity drivers.
Insights of ABC over the current overhead allocation Method:
Management accounting is the core of production and decision-making process for any company. The direct costs that are related to the units of production can be easily apportioned into the units of production but for the overheads such as cost that are not directly related to the product, such as the machine serving costs and others alternative costing is to be used. For the allocation of the overheads, two methods are applied those are
• Traditional costing
• Activity-Based Costing
The use of traditional costing is very easy to allocated and inexpensive accounting practice. Whereas ABC costing is comparatively cost more but give greater accuracy in cost apportionments. In the traditional costing method, the overheads cost is being added by predetermined overhead rates which are added to the direct cost of manufacturing. The traditional method is prominent to use for the small-scale companies and production houses, where the overheads costs are comparatively low in terms of the direct cost of production. For the larger companies, the ABC cost allocation tool is desired as the overhead costs are being very high compared to the cost of direct materials. Further, in large scale organizations, the cost is a bit complex to measure and allocate. In such cases, the ABC identifies all of the specific consumptions of the overheads that are related to various manufacturing units. The product overhead allocation is different for different products. Therefore, it will not be reasonable to apply the same overhead costs to all products. To solve those difficulties the ABC costing is being made. The fundamental difference between the traditional and Activity-based costing is that in ABC technic the indirect pools are created consisting of the similar category of the product cost, for instance, the production and setup cost for Wilkerson and such costs are allocated to specific productions. Therefore, Wilkerson can ascertain the profitability and production-related decision regarding the current productions with the help of the Activity-based costing.
Cost Allocations rates at full capacity:
There are two types of cost allocation, is that the cost allocated based on the actual capacity and cost allocation as per full capacity. The computation method will be the same for those two capacities however the result will be different. This is computed that who the cost estimated for the manufacturing of the product Valves, Pumps and Flow controls with the actual number of productions. In a general scenario, the production is not similar to the budgeted number of productions, but overheads cost will remain the same extensively. Therefore, the cost of the ABC method as per full capacity rates and the actual capacity rates will forecast the different cost. This will showcase the production efficient and there effects on the products. The full capacity cost driver will be shown in appendix 1.
Wilkerson decision to use actual capacity or full capacity costs under the ABC method
The full capacity cost is calculated to estimate the production requirements for the company and most importantly, to examine the performance evaluations. Additional this will be useful in asserting the product deficiency of the company. In the relative case, the company is lacking behind the profit. Therefore, the management is considering to review the production cost. As per which it is being ascertained that the actual consumption for machine-hours, production run units are relatively low compared to the full capacity of operations. Therefore, the actual cost will be higher than the full capacity costs of overheads per unit. As per the actual capacity ABC allocation, the total cost of the products is $46.17, $58.20 and $115.38 for the products valves, pumps and Flow control. It identifies that the product Flow control is quoted low compared to the cost of production. (please refer to appendix 2)
Suggestion:
Therefore, the company may either discontinue the production are increasing the price of the product. In the case, as the company is projecting a gross margin of 35% for each product than in that case a mark up of 35% plus the cost of flow will be able to contribute as per the needs of the company. This will increase the profitability of the company and make a barrier in the downtrend of the profitability for Wilkerson. Based on the market condition and limited threats of competition, it is advisable to increase the cost of the Flow Control as there is significant future growth in the future. Therefore, the increase in the price of Flow control will not make any business loss for the company. Although, the company may cover the cost only profits from the flow controllers to make great market control and eliminates the chances of penetration of competitors in the future. As the company is generating more than the desired limits for product Valves and Product Pups with an increase of 12.3% (47.9%-35%) and 0.8% (35.8%-35%) respectively it will coverup the low contribution of the Flow Control. This will be effective in the future performance of the company as we will control a major market share as well as outscoring the current and future competitions.
In this memorandum, all ethical practice regarding the cost control is measured, and their effectiveness in production cost, cost estimation along with the pricing strategies. For any assistance, feel free to contact, and errors and omissions are solicited.
Thanking You,
Date:
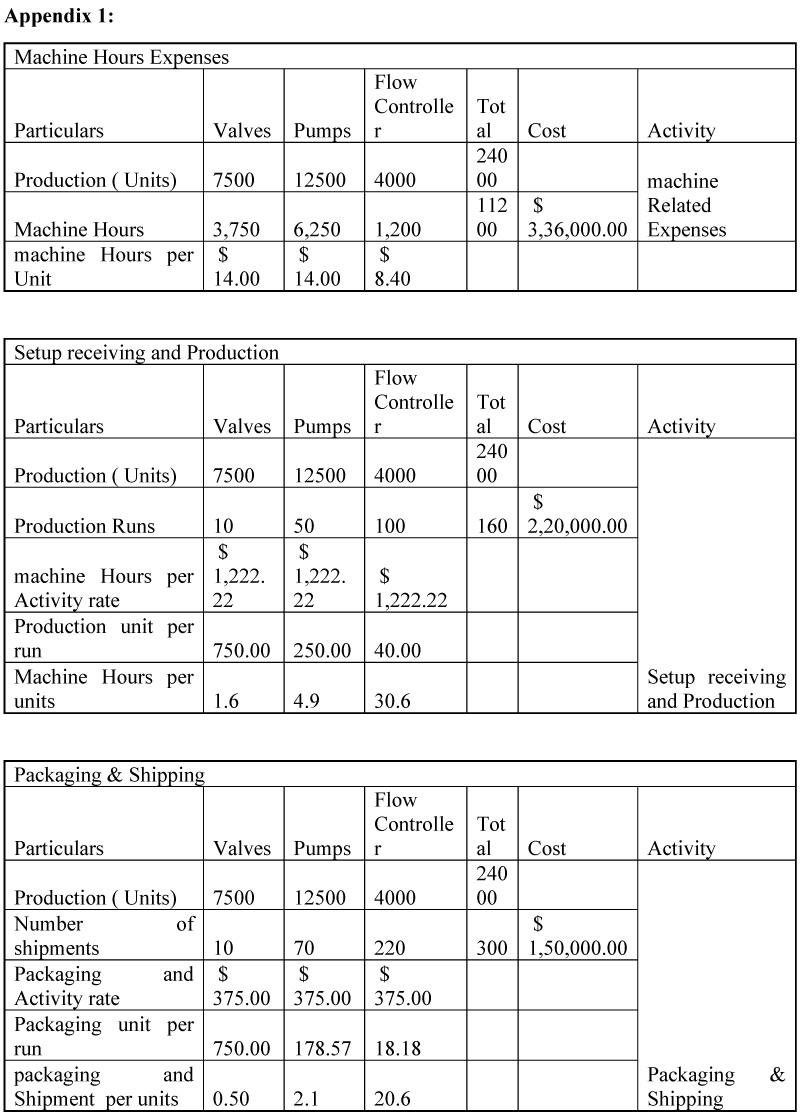
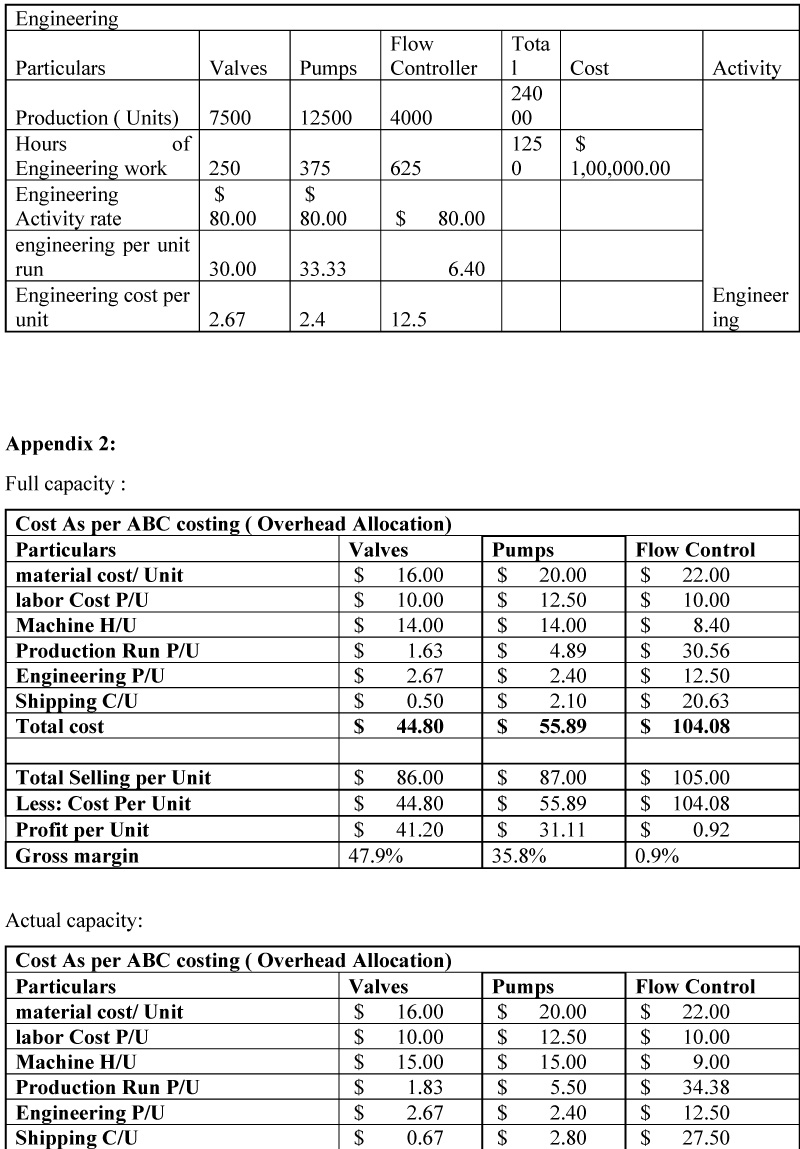
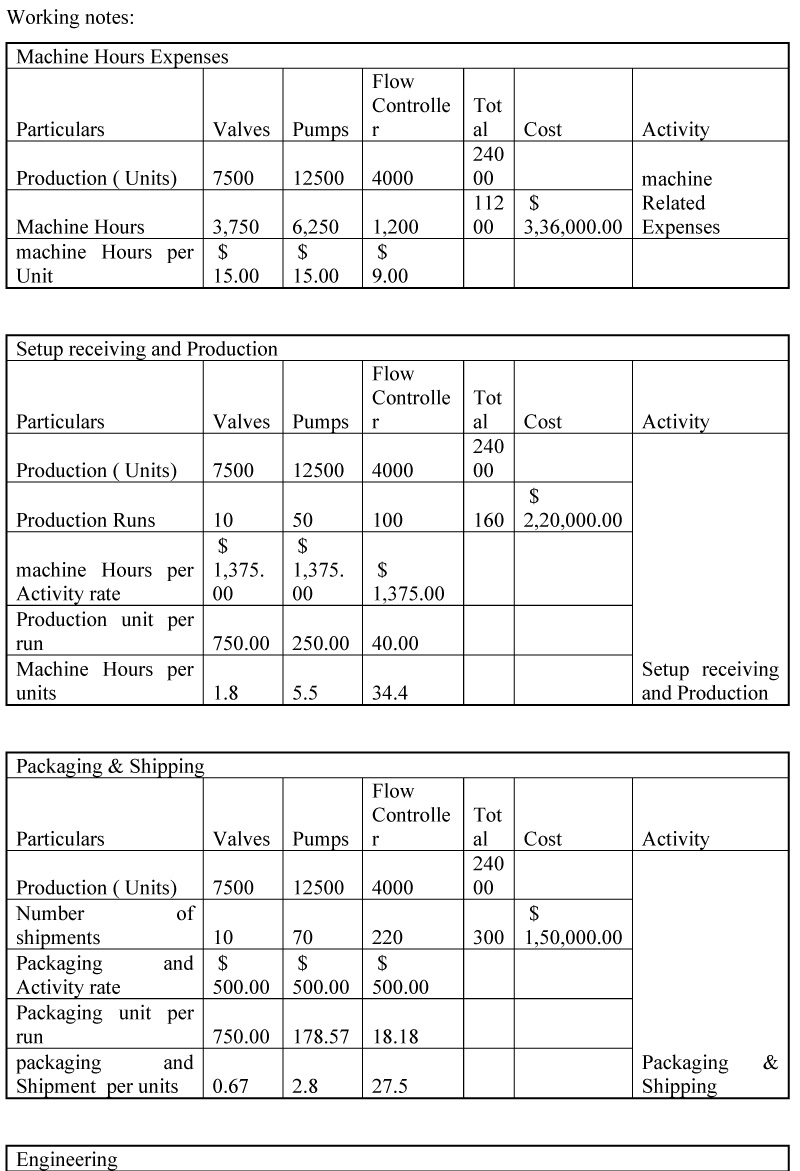